Unlocking the Potential of Butt Fusion Machines for Welding HDPE Pipes
Butt fusion machines have become an essential tool in the welding of High-Density Polyethylene (HDPE) pipes. These machines offer a reliable and efficient method of joining pipes together, creating strong and durable connections. However, many professionals in the industry are not fully aware of the capabilities and potential of butt fusion machines. This blog aims to unlock the true potential of these machines and provide valuable insights into their usage, benefits, and best practices for welding HDPE pipes. Whether you are a seasoned professional or a newcomer to the industry, this blog is a must-read for anyone looking to optimize their pipe welding processes.
Understanding the importance of high-density polyethylene (HDPE) pipes
HDPE pipes are gaining popularity in various industries due to their unique characteristics and numerous advantages. Understanding the importance of HDPE pipes is crucial in unlocking the full potential of butt fusion machines for welding them.
HDPE pipes are known for their exceptional strength, durability, and flexibility. They are resistant to corrosion, chemicals, and UV rays, making them suitable for a wide range of applications including water supply, drainage systems, gas distribution, and more.
Moreover, HDPE pipes are lightweight, which makes transportation and installation easier, saving both time and cost. Their smooth interior surface ensures excellent hydraulic characteristics, reducing energy consumption and minimizing pressure loss.
By recognizing the importance of HDPE pipes, professionals can make informed decisions about the type of pipe to use and the appropriate butt fusion machine settings for achieving impeccable welds.
The advantages of butt fusion machines for welding HDPE pipes
Butt fusion machines play a crucial role in the welding process of HDPE pipes, offering several advantages that ensure reliable and durable welds. One of the key advantages is the ability to produce a seamless joint, resulting in a leak-free and robust connection. This is especially important in industries such as water supply and gas distribution, where any leaks could have serious consequences.
Furthermore, butt fusion machines provide precise control over temperature and pressure during the welding process, ensuring consistent and uniform melting of the HDPE pipe ends. This results in a strong bond that maintains the structural integrity of the pipe, even under high pressure or temperature conditions.
Additionally, butt fusion machines are designed to be user-friendly, allowing operators to easily adjust the settings and monitor the welding process. This ensures efficiency and accuracy in achieving perfect welds every time.
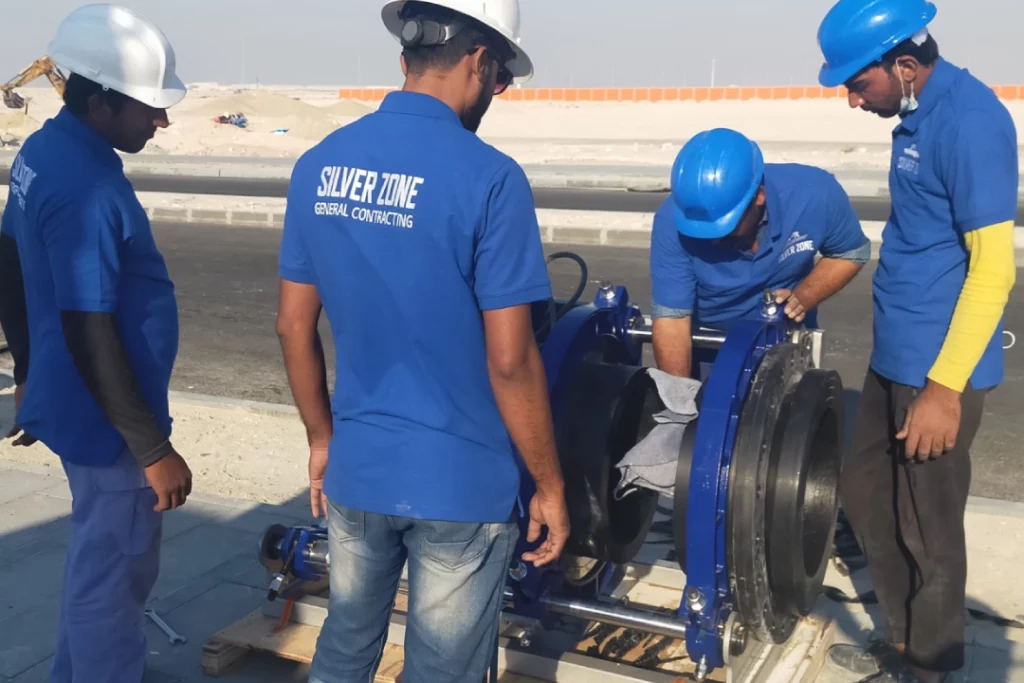
Selecting the right butt fusion machine for your project
Selecting the right butt fusion machine for your project is crucial to ensure successful and efficient HDPE pipe welding. The market offers a variety of butt fusion machines, each tailored for specific applications and project requirements.
When choosing a machine, consider factors such as the pipe diameter and material, welding pressure and temperature requirements, and the overall project scope. Different machines offer varying capabilities in terms of size range, pressure capacity, and heating element options.
It is also essential to evaluate the machine’s reliability, durability, and ease of use. Look for features such as advanced control systems, intuitive interfaces, and safety measures that ensure operator comfort and productivity.
Furthermore, consider the availability of technical support, maintenance services, and spare parts from the manufacturer or supplier. This will help minimize downtime and ensure long-term performance and reliability.
In the following sections, we will discuss the different types of butt fusion machines available and provide guidance on selecting the right machine for your specific project needs. Stay tuned for valuable insights into making informed decisions and unlocking the full potential of butt fusion machines for welding HDPE pipes.
Ensuring proper setup and safety precautions for butt fusion welding
Once you have selected the right butt fusion machine for your project, it is crucial to ensure proper setup and take necessary safety precautions to achieve successful and safe welding of HDPE pipes.
Firstly, make sure you have a clean and well-organized work area. Remove any dirt, debris, or other materials that could potentially contaminate the pipe ends or compromise the fusion process. Creating a clean environment will help ensure a strong and reliable weld.
Next, carefully align the pipe ends using the appropriate aligning tool or clamp. Proper alignment is crucial for achieving a consistent and robust fusion. Ensure that the pipes are aligned correctly, with minimal gap between the ends, to ensure a tight and secure bond.
Before starting the fusion process, it is essential to confirm that the pipe ends are clean and free from any contaminants. Clean the pipe ends using a suitable cleaning solution and lint-free cloth. This will help ensure that the fusion process is not hindered by any dirt or foreign particles.
Additionally, pay close attention to temperature and pressure settings. Follow the manufacturer’s guidelines for the specific HDPE material being used, as different materials may require different fusion settings. It is important to maintain the correct fusion temperature and pressure throughout the welding process to ensure a strong and reliable weld.
Lastly, always wear appropriate personal protective equipment (PPE) when operating the butt fusion machine. This includes safety glasses, gloves, and protective clothing. PPE will protect you from potential hazards, such as flying debris or hot surfaces, ensuring your safety during the fusion process.
By following these setup and safety precautions, you can minimize the risk of errors or accidents and achieve high-quality fusion welds.

The process of butt fusion welding with a machine
Now that we have covered the importance of setup and safety precautions, let’s dive into the step-by-step process of butt fusion welding with a machine. This process involves bringing the pipe ends together, heating them, and then applying pressure to create a strong and permanent fusion.
1. Prepping the pipe ends:
Start by preparing the pipe ends. Use a suitable cleaning solution and lint-free cloth to thoroughly clean the ends, ensuring they are free from contaminants. This will promote better fusion and prevent any weak spots in the weld.
2. Aligning the pipe ends:
Once the ends are clean, use an aligning tool or clamp to carefully align the pipe ends. Remember to minimize the gap between the ends to ensure a tight and secure bond. Proper alignment plays a crucial role in achieving a consistent and robust fusion.
3. Heating the pipe ends:
With the pipe ends aligned, it’s time to heat them. Place the heating element of the butt fusion machine between the pipe ends and apply the appropriate temperature as recommended by the manufacturer. Allow sufficient time for the heat to penetrate the pipe ends and create a molten state.
4. Removing the heating element:
Once the pipe ends reach the desired fusion temperature, remove the heating element from between the ends. Be careful while handling the hot element, and always use insulated gloves for protection.
5. Applying pressure:
With the heating element removed, quickly bring the pipe ends together to ensure a tight fit. Apply pressure using the butt fusion machine to compress and fuse the molten pipe ends. The pressure should be maintained as per the manufacturer’s guidelines, ensuring a strong and reliable fusion.
6. Cooling and trimming:
After applying pressure, allow the fused joint to cool naturally. Avoid rapid cooling methods, as they may compromise the integrity of the fusion. Once the joint has cooled, use a suitable tool to trim any excess material and achieve a neat and smooth finish.
Remember, practice makes perfect when it comes to butt fusion welding. Take the time to familiarize yourself with the process, follow proper techniques, and always refer to the manufacturer’s guidelines for your specific butt fusion machine and HDPE material.
Achieving high-quality welds and preventing common issues
To ensure high-quality welds and minimize the risk of common issues, there are a few key factors to consider during the butt fusion welding process.
Firstly, it is important to maintain the correct welding parameters. This includes maintaining the recommended temperature and pressure settings throughout the fusion process. Deviating from the manufacturer’s guidelines can result in weak welds or even failure of the joint.
Secondly, pay close attention to the cooling process. Allowing the fused joint to cool slowly and naturally will help to prevent stress cracks and ensure the joint’s strength and integrity. Avoid using cooling methods such as water or forced air, as they can cause rapid cooling and compromise the weld quality.
Thirdly, be mindful of the ambient conditions during welding. Extremely hot or cold conditions can affect the fusion process and the quality of the weld. It is advisable to perform butt fusion welding in a controlled environment to maintain consistent results.
Lastly, inspect the welded joint thoroughly after completion. Look for any signs of irregularities or defects, such as voids, cold spots, or uneven fusion. If any issues are identified, take appropriate measures to rectify them, such as rewelding or replacing the joint if necessary.
By following these guidelines and considering these factors, you can significantly increase the chances of achieving high-quality butt fusion welds with your HDPE pipes. In the next section, we will discuss the importance of regular maintenance and calibration of butt fusion machines to ensure optimal performance and longevity. Stay tuned!
Regular maintenance and care for your butt fusion machine
Regular maintenance and care for your butt fusion machine is essential to ensure its optimal performance and longevity. Neglecting routine maintenance can result in decreased efficiency, increased downtime, and potential breakdowns.
To start, it is crucial to clean the machine regularly. Remove any debris, dirt, or residue that may have accumulated on the heating plate or other components. Use a soft cloth or brush and a mild cleaning solution to avoid damaging the machine.
Additionally, inspect the machine for any signs of wear or damage. Check the heating element, clamps, and hydraulic system for any leaks, cracks, or malfunctions. Replace any worn or damaged parts promptly to avoid compromising the quality of your welds.
Calibration is another critical aspect of maintaining a butt fusion machine. Regularly check the temperature and pressure gauges to ensure they are accurately measuring the parameters. If any discrepancies are identified, recalibrate the machine to ensure precise control during the fusion process.
Lastly, keep a record of all maintenance and calibration activities. This will help you track the machine’s performance over time and schedule future maintenance tasks more effectively.
By following these maintenance and care practices, you can maximize the lifespan of your butt fusion machine and ensure consistent, high-quality welds.
The future of butt fusion machines in the HDPE pipe industry
As technology continues to evolve, so does the potential of butt fusion machines for welding HDPE pipes. The future looks promising, with advancements aimed at improving efficiency, accuracy, and ease of use.
One of the key areas of development is automation. Manufacturers are incorporating advanced features such as touchscreen interfaces, programmable settings, and real-time monitoring systems. This not only simplifies the welding process but also enhances quality control by ensuring precise temperature and pressure control.
Another area of focus is portability. Innovations in design and materials are making butt fusion machines more lightweight and compact without compromising performance. This opens up new possibilities for on-site welding applications, reducing the need for transporting pipes to a fabrication facility.
Furthermore, the integration of smart technology is revolutionizing the industry. Imagine a butt fusion machine equipped with sensors that detect and prevent errors, provide real-time feedback, and generate comprehensive welding reports. This level of automation and data analysis would streamline operations, enhance productivity, and enable proactive maintenance.
In conclusion, the future of butt fusion machines in the HDPE pipe industry is bright. Advancements in automation, portability, and smart technology present exciting opportunities to unlock even greater potential in terms of efficiency, accuracy, and overall performance. Stay tuned for our next blog section, where we will delve deeper into these emerging trends and their potential impact on the industry.
Conclusion: Leveraging the potential of butt fusion machines for efficient and durable HDPE pipe welding
Leveraging the potential of butt fusion machines for efficient and durable HDPE pipe welding is crucial in ensuring successful and reliable installations. In this blog series, we have explored various aspects of the advancements in butt fusion technology and their impact on the industry.
Automation has emerged as a key driver of efficiency, accuracy, and quality control in the welding process. With advanced features like touchscreen interfaces and real-time monitoring systems, welders can enjoy greater control over temperature and pressure, resulting in consistently high-quality welds.
Portability has also become a significant consideration in butt fusion machine design. The ability to easily transport and set up machines on-site reduces the logistical challenges of moving heavy pipes to fabrication facilities. This increases flexibility and decreases project timelines, ultimately saving time and costs.
Lastly, the integration of smart technology has revolutionized the industry, allowing for proactive maintenance and optimization of operations. Machines equipped with sensors and data analysis capabilities provide real-time feedback, detect errors, and generate comprehensive welding reports. This level of automation not only streamlines operations but also improves productivity and ensures proactive maintenance.
As the butt fusion machine industry continues to evolve, it is crucial for industry professionals and stakeholders to stay informed and adapt to these emerging trends. By utilizing the full potential of butt fusion machines, we can achieve more efficient and durable HDPE pipe welding, setting new standards for quality and performance in the industry.